Glacier Coolant VS Ethylene Glycol
Inhibited Heat Transfer Fluid Protection
Corrosionis the enemy of any water-based system, but a properly balanced and inhibited glycol system can protect equipment without the loss of thermal performance. Glacier Coolant is the industry leader in high-performance inhibited glycol fluids.
Uninhibited Glycol & The Hidden Dangers
Glycol fluids provide excellent thermal properties for water-based HVAC or cooling systems by significantly reducing the freeze point of water. Without glycol, these systems would seize up & expand dramatically, leading to deformed pipes or burst connections.
However, glycol chemistry can degrade overtime leading to the formation of organic acids especially if the fluids are exposed to high temperatures. Along with the formation of acid, there are several components that can lead to challenges:
Heat – Oxygen – Chlorides – Sulfates – Metallic Impurities – Contaminants
The presence of these acid byproducts can reduce the overall pH of the system resulting in higher corrosion rates and system damage. Without the proper concentration of inhibitors in the fluid the metal surfaces are left unprotected, and the initial savings on the home-brew fluid become a drop in the bucket compared to the costs incurred to repair or replace the system itself.
Disadvantages inherent to uninhibited ethylene glycol, including:
- It is relatively easy to degrade.
- It promotes corrosion after it degrades.
- It is difficult to monitor.
- It sorbs water from the atmosphere.c
These disadvantages can lead to frequent fluid changing, which can cost users money in labor and parts. There also can be lost production costs due to shutdown and possible premature failure of the system.
Glacier Coolant Heat Transfer Fluids Solutions
Glacier Coolant has decades worth of proven performance in expertise in the thermal fluid industry. Their specially engineered inhibitor packages ensure excellent protection from corrosion and best-in-class long term operation.
Advantages of Glacier Coolant Heat Transfer Fluids
What are Glacier Coolant Heat Transfer Fluids? Ethylene or Propylene glycol-based liquids with our signature corrosion inhibitors for optimum system performance, Glacier Coolant offers a full range of Glacier Coolant Heat Transfer Fluids to meet your specific system requirements.
Long-lasting performance
Glacier Coolant Heat Transfer Fluids are also long-lasting and can be operated for many years in properly maintained systems. Their special corrosion inhibitor package supports higher temperature operation compared to alternative technologies.
Corrosion protection
Glacier Coolant Heat Transfer Fluids are formulated with carefully chosen corrosion inhibitors to provide protection to the metallic parts of process equipment, therefore improving process efficiency and reducing maintenance costs. Glacier Coolant Heat Transfer Fluids are very efficient at protecting aluminum.
Glacier Coolant Heat Transfer Fluids are made for a very broad range of applications. The specially formulated inhibitor packages of Glacier Coolant Heat Transfer Fluids are effective in minimizing corrosion of a wide variety of metals that are used in industrial and residential applications, reducing maintenance costs and extending the life of the process equipment.These inhibitors minimize corrosion of metals in two ways.First, they passivate the surface of metals, reacting with the surface or forming a layer on the surface to prevent acids from attacking it. Second, the inhibitors in Glacier Coolant Heat Transfer Fluids buffer any acids formed as a result of glycol oxidation. All glycols produce organic acids as degradation products. This degradation is accelerated in the presence of oxygen and/or heat. Left in solution, acids lower pH and contribute to corrosion. Properly formulated inhibitors such as those in Glacier Coolant Heat Transfer Fluids neutralize these acids and contribute to a long fluid life time. Many commonly available coolants – such as fluids with pure organic acid technology (OAT) – have little ability to buffer these degradation products and therefore need to be changed more frequently.
Glacier Coolant Heat Transfer Fluids contain precisely formulated industrial inhibitor packages that are proven highly effective in preventing corrosion of metals commonly used in HVAC systems. And, unlike some other inhibited glycol fluids, Glacier Coolant Heat Transfer Fluidss can be easily analyzed to determine corrosion inhibitor condition. Properly maintained, Glacier Coolant Heat Transfer Fluidss may not require reinhibiting for up to 20 years.
privacy policy
This privacy policy describes how we handle your personal information. By using www.binghelengmei.com/?lang=en (the’Site”) you consent to the storage, processing, transfer and disclosure of your personal information as described inthis privacy policy.
Collection
You may browse this Site without providing any personal information about yourself. However, to receivenotifications, updates or request additional information about www.binghelengmei.com/?lang=en or this Site, we maycollect the following information:
name, contact information, email address, company and user lD; correspondence sent to or from us; any additionalinformation you choose to provide; and other information from your interaction with our Site, services, content andadvertising, including computer and connection information, statistics on page views, traffic to and from the Site, addata, IP address and standard web log information.
Use
We use your personal information to provide you with the services you request, communicate with you, troubleshootproblems, customize vour experience, inform you about our services and Site updates and measure interest in oursites and services.
Like many websites, we use “cookies” to enhance your experience and gather information about visitors and visits toour websites. Please refer to the “Do we use ‘cookies”?” section below for information about cookies and how we usethem.
Do we use “cookies”?
Yes. Cookies are small files that a site or its service provider transfers to your computer’s hard drive through youlWeb browser (if you allow) that enables the site’s or service provider’s systems to recognize your browser andcapture and remember certain information. For instance, we use cookies to help us remember and process the itemsin your shopping cart. They are also used to help us understand your preferences based on previous or current siteactivity, which enables us to provide you with improved services. We also use cookies to help us compile aggregatedata about site traffic and site interaction so that we can offer better site experiences and tools in the future.We maycontract with third-party service providers to assist us in better understanding our site visitors. These serviceproviders are not permitted to use the information collected on our behalf except to help us conduct and improve ouibusiness.
You can choose to have your computer warn you each time a cookie is beng sent, or you can choose to turn off allcookies. You do this through your browser (like Netscape Navigator or Internet Explorer) settings. Each browser is alittle different, so look at your browser Help menu to learn the correct way to modify your cookies. lf you turn cookiesoff, you won’t have access to many features that make your site experience more efficient and some of our serviceswill not function properly. However, you can still place orders over the telephone by contacting customer service.
Disclosure
We don’t sell or rent your personal information to third parties for their marketing purposes without your explicitconsent. We may disclose personal information to respond to legal requlrements, enforce our policies, respond toclaims that a posting or other content violates other’s rights, or protect anyone’s rights, property, or safety. Suchinformation will be disclosed in accordance with applicable laws and regulations. We may also share personalinformation with service providers who help with our business operations, and with members of our corporate familywho may provide ioint content and services and help detect and prevent potentially illegal acts. Should we plan tomerge or be acquired by another business entity, we may share personal information with the other company and willrequire that the new combined entity follow this privacy policy with respect to your personal information.
Access
You may access or update the personal information you provided to us at any time by contacting us at www.binghelengmei.com/?lang=en.
Security
We treat information as an asset that must be protected and use lots of tools to protect your personal informationagainst unauthorized access and disclosure. However, as you probably know, third parties may unlawfully intercepior access transmissions or private communications. Therefore, although we work very hard to protect your privacywe do not promise, and you should not expect that your personal information or private communications will alwaysremaln private.
General
We may update this policy at any time by posting amended terms on this site. All amended terms automatically takeeffect 30 days after they are initially posted on the site. For questions about this policy, please send email to us.
Why thermal fluid choice is important in pharmaceutical applications
Heat transfer systems are widely used in the pharmaceutical industry to indirectly heat and cool ingredients during processes such as bulk drug processing, batch reactions and crystallisation.
As the thermal fluid moves around the system, it transfers heat to or from base, intermediate and final stage products to achieve the required temperatures.
Thermal fluid-based systems pose many advantages compared with steam-based ones in terms of efficiency, safety and precise temperature control. However, not all thermal fluids are created equal and there are several considerations when deciding which heat transfer fluid (HTF) is most suited to a process.
Does fluid choice matter?
Upfront fluid cost may seem like a big consideration but, in the long-term, achieving good return on investment comes from maintaining the fluid appropriately. All HTFs degrade with time, but the speed of this degradation increases if system temperatures consistently exceed the recommended fluid range.
Degradation occurs at elevated temperatures because the bonds that exist between hydrocarbon chains start to break, resulting in a process known as fouling that leads to the production of carbon deposits in the system.
Eventually, sludge starts to build up inside the pipework and reduce the efficiency. The temptation here is to turn the system up to compensate for the reduction in heat transfer.
However, the Arrhenius equation suggests that increasing the temperature by just ten degrees can halve the expected lifespan of a fluid, making the problem worse.
If the thermal fluid has degraded substantially, pharmaceutical manufacturers may start to experience problems in their process and will have to cease production, throw away wasted batches and drain, clean and flush the entire system, causing unexpected and costly downtime.
Operating temperature matters
There is no need to panic, however, as thermal fluids can enjoy a very long lifespan if care is taken to select, operate and maintain them according to the manufacturer’s recommendations.
HTFs each have specific characteristics that ensure they are thermally stable and perform well if operated at the appropriate temperatures.
Even so, manufacturers should always consider their operating temperatures when selecting an HTF to ensure that the fluid can safely and efficiently run at the required temperature. As the Arrhenius equation law suggests, choosing an oil not suited to your process temperatures will cause problems later on.
Chemical considerations
HTFs have different chemical compositions that manufacturers may consider when deciding how suitable a fluid’s properties are for a specific application.
Although mineral based fluids do offer a good trade-off between cost and performance, the popular choice in pharma applications is synthetic HTFs. These have a lower susceptibility to form carbon than mineral-based oils, offer better heat transfer efficiency, thermal stability and a higher resistance to fouling.
If you are looking to operate a system at a high temperature, you might want to consider a synthetic-based fluid such as LM-15 series and LM-16 series.. Synthetic fluids are known to have better stability at high temperatures than their mineral-based counterparts.
They also have a lower viscosity than mineral-based fluids, so perform efficiently in both vapour and liquid phases. Chemical reactions and crystallisation occur at a range of low and high temperatures, so manufacturers can benefit from choosing a thermal fluid with a broad operating temperature range, such as Globaltherm L and Globaltherm J.
These fluids also have low viscosity that allows the fluid to be easily pumped around the system, improving heat transfer efficiency and reducing production energy costs.
A full fluid life
However, once you have chosen a suitable fluid, you can’t stop there. All thermal fluids will degrade with time, but regular monitoring and maintenance will slow the process.
Implementing a comprehensive thermal fluid lifecycle maintenance plan further supports manufacturers with on-site engineering and thermal fluid management support from experts in heat transfer oil.
Regular thermal fluid analysis can also slow degradation. By taking a representative sample from a system that is hot, live and circulating and sending it for laboratory analysis, pharmaceutical manufacturers can understand the condition of their fluid and plan maintenance accordingly.
Preventive maintenance can help to slow degradation and reduce the risk of carbon deposition and fouling from decreasing the efficiency of the HTF. This way, manufacturers can optimise system performance, reduce energy costs, improve health and safety and decrease unexpected downtime.
The best approach is to implement a comprehensive thermal fluid lifecycle maintenance plan, such as Thermol care 24/7 Live Condition Monitoring.
This cloud-based remote monitoring system uses real-time analytics to monitor fluid condition, sending instant alerts to maintenance personnel on a smart device as soon as it detects any issues that could impact productivity.
Ultimately, a manufacturer must consider the heat transfer performance against their manufacturing requirements. Poor fluid choice can lead to inefficient system operation and accelerated thermal fluid breakdown, which can increase maintenance requirements and mean products are non-compliant.
However, by carefully considering the requirements of the system and the application, manufacturers can make informed choices about their heat transfer fluids and ensure smooth operation throughout the fluid’s working life.
How to Choose the Right Heat Transfer Fluid
Heat transfer fluid selection can involve complicated, multi-dimensional decisions where factors such as thermal stability,pumpability, pressure requirements, and more must be weighed in an effort to achieve the optimum balance of performance and economy in your particular system. However, you may be able to narrow your range of options with a few basic decisions.
First, choose a synthetic organic fluid, a silicone fluid or an inhibited glycol-based fluid based on your temperature requirements. If your heat transfer application has a maximum-use temperature requirement above 175˚C (350˚F), consider a synthetic organic or silicone fluid. For temperatures lower than 175˚C (350˚F), or if you need freeze protection for a water based system, consider an inhibited glycol-based fluid.
Synthetic organic and silicone fluids are thermally stable at temperatures up to 400˚C (750˚F). While operating at these elevated temperatures, they exhibit vapor pressures much lower than steam, making them more practical and less expensive to use. Fluids with broad operating temperature ranges offer high temperature stability and low temperature pumpability.
Inhibited glycol-based fluids are solutions of water and inhibited glycols operating below 175˚C (350˚F). The concentration of glycol in the fluid directly affects its performance properties.
If an inhibited glycol-based fluid will meet your system’s thermal requirements, you can choose between ethylene glycol- and propylene glycol-based fluids. In most applications ethylene glycol-based fluids are preferred because of their lower viscosity and resulting superior heat transfer efficiency.
However, local regulations or a specific application may require the use of a propylene glycol-based fluid. Propylene glycols are commonly used in applications in which a fluid low in acute oral toxicity is required, for example, where incidental contact with drinking water is possible and in food processing applications.
What is the difference between propylene glycol and ethylene Glycol?
How do you choose a glycol?
Glycols are used in many different process cooling and heating applications: HVAC systems, ice rinks, food and pharmaceutical processes,Chemical processes, plastic molding, and solar thermal heat transfer. There are two main types of glycols: ethylene glycol and propylene glycol.
The number one difference between the two glycols is that ethylene glycol is toxic and propylene glycol is not, allowing propylene glycol to be purchased as food grade in addition to the technical or industrial grade.
The two glycols also have differences in their physical properties. Propylene glycol solutions have higher viscosity and higher freezing point than ethylene glycol at the same percentage, causing it to be less thermally efficient than ethylene glycol, especially at lower temperatures. Propylene glycol is also more expensive than ethylene glycol.
To illustrate this, compare the properties of 50 volume % propylene glycol versus ethylene glycol. 50% propylene glycol has a freezing pointof -31°F, where 50% ethylene glycol freezes at -36°F. The viscosity of that propylene glycol solution is 96 centipoise at -10°F, and the ethylene glycol will be 27 centipoise at the same temperature. This means that ethylene glycol can be used at temperatures roughly 20 degrees lower than propylene glycol.
For these reasons, ethylene glycol is commonly used in applications where efficiency is important and there is no human or animal contact, such as ice rinks, plastic molding, and in-line heaters,pharmaceutical processes,Chemical processes. Ethylene glycol is the predominant fluid used for automotive antifreeze formulations. Propylene glycol is used in food and pharmaceutical applications, and HVAC systems in schools, homes, and businesses – anywhere there is a risk of human or animal exposure.
To determine which glycol is most appropriate for your system, all these factors should be taken into consideration: type of application, toxicity, thermal efficiency, and cost. There is no one-size-fits-all solution when it comes to constructing a heat transfer system, and you should make your choice of fluid thoughtfully and carefully.
What are Phase Change Materials (PCM)?
You’ve likely come across the term Phase Change Materials (PCM) and wondered, “What exactly are PCM, and why is there such a push for them as a sustainable solution?” Let’s explore the essence of PCM—they are substances with the unique capability to absorb or release energy during a phase transition. This exceptional quality enables PCMs to smoothly shift between solid and liquid states, effectively storing and releasing thermal energy in the process.
How Does It Work
When you heat a solid PCM, it turns into a liquid, absorbing a lot of heat energy in the process. Similarly, when you cool a liquid PCM, it turns into a solid, releasing the stored heat energy. This ability to absorb and release heat without changing its temperature is what makes PCM so special.
Let’s consider an everyday example: ice turning into water. To melt ice, it requires a considerable amount of energy (334 joules per gram, to be precise). However, once it becomes water, it only needs 4.18 joules per gram to raise its temperature by one degree Celsius. This stark contrast illustrates the unique capability of PCMs in absorbing and releasing energy.
Types of Phase Change Materials
Phase Change Materials can be categorized into three main types: Organic, Inorganic, and Eutectic.
Organic PCMs: Organic PCMs are made from paraffin and non-paraffin materials, such as petroleum, plants, or animals. Paraffin wax is a notable example. These PCMs are preferred for their low cost, chemical stability, and ease of availability.
Inorganic PCMs: Inorganic PCMs like metallic alloys and salt hydrates utilize minerals and natural salts, providing high latent heat capacity and thermal conductivity, making them ideal for various applications.
Eutectic Mixtures: Eutectic PCMs are innovative blends of different materials, carefully designed to achieve specific melting points and optimize energy storage capabilities.
Sustainability of PCM
Phase Change Materials (PCMs) are considered sustainable due to their ability to enhance energy efficiency, reduce overall energy consumption, and integrate with renewable energy sources. They contribute to a more stable and reliable energy supply, extend the lifespan of products, and often involve non-toxic and environmentally friendly materials. The adaptability of PCMs in various applications makes them versatile tools for improving sustainability and minimizing environmental impact.
Applications and Impact
Phase Change Materials find diverse applications, with the following examples representing just a few available options that Pluss Advanced Technologies has to offer.
Medical Sector: PCM-based products are utilized in the healthcare field for temperature-controlled shipping of medications, vaccines, and other sensitive medical supplies. Maintaining the required temperature ensures the efficacy and safety of these products during transit.
Energy-efficient Buildings: PCM-enabled building materials regulate indoor temperatures by absorbing the excess heat during the day, releasing it at night, and vice versa. This strategic thermal management minimizes the reliance on continuous heating or cooling, resulting in substantial energy savings.
Transportation: Phase Change Material (PCM) technology finds application in cold chain logistics, especially in passive refrigerated vehicles, maintaining the right temperature for perishables. By minimizing the dependency on active cooling during transport, PCMs enhance energy efficiency and environmental sustainability in the transportation of perishable goods.
Solar Energy Solutions: In the realm of renewable energy, PCMs play a pivotal role. They are integrated into solar water heaters, largely increasing their storage capacity, ensuring a steady supply of hot water even when the sun is not shining.
Challenges and Future Innovations
While Phase Change Material technology has made remarkable strides, challenges such as material cost, encapsulation techniques, and durability persist.
Researchers and scientists around the world are tirelessly working on overcoming these hurdles, envisioning a future where PCM applications become even more widespread and impactful.
Transforming the Future with Phase Change Materials
From enhancing the energy efficiency of our homes to paving the way for greener transportation solutions, PCMs are at the heart of a sustainable future. With continued research and innovation, these materials will undoubtedly shape a world where energy conservation meets unparalleled efficiency, ensuring a brighter, eco-friendly tomorrow for generations to come.
Glacier Coolant Technology (Beijing) Co., LTD. Related products:
phase change refrigerant:
LM-XL-1
LM-XL-2
LM-XL-3
LM-XL-4/p>
phase change heat storage agent:
LM-XR-1
LM-XR-2
LM-XR-3
Discussion on construction technology of hydrogen refueling station
There is no hydrogen production unit in the external hydrogen supply hydrogen refueling station. Hydrogen is transported from the hydrogen plant to the hydrogen refueling station through long tube trailers, liquid hydrogen tankers or hydrogen pipelines, compressed by the compressor and transported to the high-pressure hydrogen storage bottle for storage, and finally filled into fuel cell vehicles through the hydrogen dispenser.
According to different hydrogen storage modes, it can be further divided into high-pressure gas hydrogen station and liquid hydrogen station,About 30% of the world’s liquid hydrogen storage and transportation stations are hydrogen refueling stations, which are mainly distributed in the United States and Japan. At present, China is all high pressure gas hydrogen stations.Compared with the gas hydrogen storage and transportation, the liquid hydrogen storage and transportation hydrogenation station occupies a smaller area and has a larger storage capacity, but it is also more difficult to construct, which is suitable for large-scale hydrogenation.
Fig. 1 Technical Route of External Hydrogen Supply and Hydrogenation Station
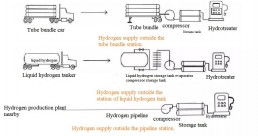
The internal hydrogen production and hydrogenation station is equipped with a hydrogen production system. The hydrogen production technologies include hydrogen production by electrolysis of water, hydrogen production by natural gas reforming, and hydrogen production by renewable energy. The hydrogen produced in the station generally needs to be purified, dried, and then compressed, stored, and injected.Among them, electrolytic water hydrogen production and natural gas reforming hydrogen production technologies are most widely used in the station hydrogen production and hydrogenation stations because of the ease of equipment installation and high degree of automation, and the natural gas reforming technology can be developed based on the construction of natural gas infrastructure. The European hydrogen production and hydrogenation stations mainly use these two hydrogen production methods.
Fig. 2 Technical route of internal hydrogen production and hydrogenation station
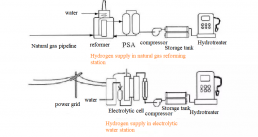
According to different hydrogen supply pressure levels, the hydrogen refueling station is divided into two types of hydrogen supply pressure: 35MPa and 70MPa.
Most foreign markets use 70 MPa,Restricted by the development of existing compressor and hydrogen storage bottle technologies, most domestic hydrogen refueling stations use 35 MPa.When 35 MPa pressure is used for hydrogen supply, the working pressure of the hydrogen compressor is 45 MPa, and the working pressure of the high-pressure hydrogen storage cylinder is 45 MPa;When 70 MPa pressure is used for hydrogen supply, the working pressure of the hydrogen compressor is 98 MPa, and the working pressure of the high-pressure hydrogen storage cylinder is 87.5 MPa.
On the basis of the original or new gas station and gas station, add hydrogenation functional facilities to make the station have multiple functions such as refueling, gas refueling, hydrogenation, etc.According to the Technical Code for Hydrogenation Station (GB 50516-2010), the hydrogen refueling station can be built in a single station, requiring relocation and high input cost;The oil hydrogen hybrid station is the development direction of the future hydrogen refueling station, which can also avoid the need for more space and time for electric vehicle charging.
Glacier coolant provides customers with coolant to ensure that the temperature is kept at – 40 ° C when hydrogen is injected, alleviate the temperature rise of pressure drop, and is widely used in hydrogen refueling stations.Through long-term research, our company has invented glacier coolant products and applied for national patents.He has successively invented “M3 super film rust prevention” technology, “Modify2000 composite modification” technology and “Box7 all-around test”.The problems such as corrosion of equipment, narrow temperature range and potential safety hazards caused by salt water, ethylene glycol and dichloromethane, which are substitutes of traditional coolant, have been solved.In addition to hydrogen refueling stations, they are also widely used as industrial low temperature load coolant, pharmaceutical high and low temperature load coolant, industrial antifreeze, central air-conditioning antifreeze, solar antifreeze, automobile antifreeze, laser antifreeze, etc.
Application of Glacier coolant Modified Polyfluorochemicals in the Industry
Immersion cooling of power devices
From high-speed electric trains to wind turbines, to electric motors in heavy bulldozers and personal electric vehicles (EVs),The ability to control voltage accurately on a large scale makes many efficient and powerful innovative ideas possible.However, the devices that manage this process, such as power inverters, thyristors, variable speed drives and other power devices, need to be efficiently cooled.
Glacier coolant modified polyfluorochemicals can be used as an ideal immersion cooling working fluid for variable voltage power devices.These insulating liquids can safely contact electronic equipment, and can achieve efficient and uniform cooling of power devices by using single-phase or two-phase immersion cooling.These liquids have a wide operating temperature range, excellent material compatibility and easy maintenance, making the immersion cooling method based on the Glacier coolant modified polyfluorochemicals an excellent alternative to the air, water or oil cooling method. The product achieves all of these properties without compromising on worker safety or environmental sustainability.
The progress of power devices has pushed the whole world forward.Our modified fluoride solution can keep these equipment cool by simple, efficient and high-performance immersion cooling.Compared with the existing cooling methods, the immersion cooling of glacier coolant modified fluoride solution has obvious advantages. It can be considered for future power device applications, such as high-speed railways, heavy machinery, wind turbines, high-speed elevators, and automobiles.
Data center cooling
The rise of data economy has fundamentally changed people’s lifestyle;Moreover, the current world is always online and highly integrated, which is driving enterprises to operate at a faster and faster speed.Almost all aspects of people’s daily life depend on the tasks running inside the data center.However, the operation of these data centers requires high costs in terms of energy consumption, water use, floor space, etc.Obviously, what we need is a faster, smarter and more sustainable data center. By transferring the data center from traditional cooling mode to submerged liquid cooling using glacier modified polyfluorochemicals, enterprises can manage the impact on costs and natural resources.
Glacier coolant modified polyfluorochemicals can be used in the following systems:
Large scale data center
No matter where you decide to locate, you can deploy a data center with a more consistent cooling infrastructure worldwide.Reducing or eliminating air cooling infrastructure (such as chillers, telecommunications/network equipment, facility floor space, etc.) to a greater extent can meet new workload demands while reducing capital expenditure.With the improvement of cooling efficiency, the cost of special power required for auxiliary cooling will be reduced.Reduce the power efficiency index (PUE) and the use of water resources. When the power efficiency index is as low as 1.03, a more energy efficient and sustainable data center can be built.
Supercomputing Center
By increasing power efficiency, immersion cooling can now support new or more compute intensive workloads that are difficult to cool in an efficient and cost-effective manner with traditional cooling solutions. Reduce operating expenses. With the improvement of cooling efficiency, the cost of special power required for auxiliary cooling will be reduced.
Enterprise High Performance Computing
Support new or more compute intensive workloads that are difficult to cool in an efficient and cost-effective manner with traditional cooling solutions. Lower latency. Delay sensitive workloads can be run in more intensive, space optimized data centers, or closer to users’ server cabinets to help reduce latency. Improve hardware reliability. The lower chip junction temperature, the reduction of temperature fluctuations and hot spots improve the operation reliability; At the same time, the necessary moving parts in traditional cooling methods are reduced to a large extent, thereby reducing common hardware failures.
Application of Glacier Coolant Modified Polyfluorochemicals in Insulating Gas, Thermal Control and Fire Extinguishing
Insulating gas for power industry
Make meaningful changes for the future of the earth.Replace sulfur hexafluoride with insulating gas, a powerful greenhouse gas, which is usually used for insulation and protection of medium voltage and high voltage transmission and distribution infrastructure.
The power grid is a way for us to rapidly improve the quality of life. Its reliability is crucial, and no error is allowed.Although the electric power industry brings safety and comfort to human beings and improves productivity, if sulfur hexafluoride leaks or accidentally releases, it will produce significant greenhouse gas effects, thus affecting the nvironment.
Therefore, scientists are concerned about the demand for insulating gas in the power industry. After a lot of development and testing, insulating gas came out.This insulating gas is often used in a gas mixture, its performance is equivalent to or improved, and its impact on the environment can be reduced. If you are looking to build a more environmentally friendly grid, we can help.
Considering the dielectric properties and reliability of sulfur hexafluoride, the power industry has been willing to use it as an insulating gas to meet relevant challenges.However, sulfur hexafluoride is a powerful greenhouse gas, and its global warming potential is 23500 times that of CO2 in a 100 year cycle.In fact, it is the most powerful greenhouse gas recognized by the Intergovernmental Panel on Climate Change (IPCC) so far.Therefore, glacier coolant cooperates with industry leaders to develop alternative solutions using fluoride insulation gas, which can reduce the impact of greenhouse gases by 99.99%.
Fire fighting
Use fire extinguishing systems to improve the year-round protection system, protect your key assets, maintain business continuity, help protect life and protect the earth.When you choose the fire extinguishing system based on glacier modified fluoride, you will choose the most advanced fire extinguishing science with excellent performance and high safety without harming the environment.Glacier modified fluoride extinguishing agent can work in the most challenging environments, such as data center, control room, museum, etc., to help protect your assets and personnel safety.In case of fire, this fire extinguishing cleaner can operate continuously, which helps to minimize the downtime for recovery and cleaning.In addition, it does not consume the ozone layer, the global warming trend (GWP) is less than 1, and the atmospheric life is short. It is not the goal of phasing out HFC, so it is an ideal long-term choice for the global environment and commercial development.The fire extinguishing agent is stored in liquid form and becomes gas when released. It will float to the affected area quickly and extinguish the fire quickly by absorbing heat. It will not harm workers or cause water damage.
Thermal control
Nowadays, many advanced technologies have to do the same thing: thermal management. Whether it is the temperature control in the semiconductor chip manufacturing process, or the heat dissipation in the data center, power devices, and avionics, heat transfer widely exists in modern life.
Glacier coolant improve people’s lives with the help of science.Fluorinated fluids can not only provide excellent performance in many heat transfer applications, but also have no negative impact on personal safety and environmental sustainability.Fluoride liquid is a nonflammable insulating liquid. It has the characteristics of wide working temperature range, easy maintenance and cleaning. It is a substitute for traditional cooling liquid (such as water, water glycol or oil).Fluoride liquid has a wide range of applications, from cold plate cooling of semiconductors to immersion cooling of data centers to spray cooling of avionics.
How Glacial Coolant Liquid Helps Data Center Implement Energy Conservation and Emission Reduction Plan
In the total global carbon emissions, the contribution of information and communication technology equipment will reach 14% by 2040, accounting for more than half of the carbon emissions of transportation. The energy consumption of data centers accounts for a large part of it.In the environment of energy conservation and emission reduction in the whole society, manufacturers and users pay more and more attention to the energy conservation and emission reduction of data centers.
Figure 1 Climate Warming and Ecological Catastrophe in 2100
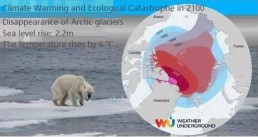
Is it a bit shocking to see Figure 1?While mankind enjoys the convenient life brought by industrialization, it also brings a heavy burden and serious environmental pollution to the earth. The excessive emission of carbon dioxide has led to global warming.Due to the rising temperature, the area of Arctic glaciers is decreasing year by year. It is predicted that by 2100, there will be only a small area in the middle.At that time, the Arctic glaciers will almost disappear, and the precious polar bears will have nowhere to live.The sea level will rise by 2.2M, some islands and coastal cities will be submerged, and the land on which our human beings depend will become smaller.The nearby Beidaihe Beach and the Maldives, thousands of miles away, may only be preserved in photos.Climate change also has a significant impact on the global natural ecosystem. In addition to temperature rise, extreme weather events also occur frequently, which brings severe challenges to human survival and development.
Figure 2 Trends in world carbon dioxide emissions
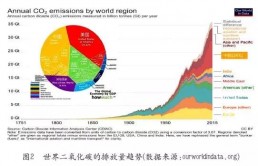
Figure 2 shows the trend of carbon dioxide emissions.In the past 150 years, with the process of industrialization, global carbon dioxide emissions have increased dramatically.From 1950 to 2015, the global carbon dioxide emissions increased rapidly, which is also a stage of rapid development of China’s economic construction.By 2015, China’s GDP had exceeded 14% of the total world GDP,What percentage of carbon dioxide emissions does 14% of GDP correspond to?As shown in the figure,The proportion of carbon dioxide emissions in China has accounted for 24% of the world,The comparison between 14% and 24% data is obviously out of proportion. Although there are elements of economic structure, it also shows that China has a heavy task of energy conservation and emission reduction. We have a long way to go, which requires our joint efforts to protect the environment on which we and future generations depend.
In the face of global warming, the United Nations has also held climate change conferences many times to discuss strategies to curb warming.At the 11th United Nations Climate Conference and the 21st Conference of the Parties, China put forward its goal of independent contribution.The achievement of national goals cannot be separated from the contribution of each enterprise.When it comes to supporting the national energy conservation and emission reduction goals and reducing carbon emissions, we usually believe that high pollution and high energy consumption industries such as petroleum, chemical industry and steel smelting are the main “culprits” of carbon emissions.Recently, researchers from McMaster University in Canada released a new study that overturned the public’s perception.Researchers believe that,Information and communication technology products such as smart phones are also one of the drivers of global warming.In the total global carbon emissions,The “relative contribution” of ICT equipment will increase from 1% in 2007 to 3.5% in 2020, and will eventually reach 14% in 2040, accounting for more than half of transportation carbon emissions.The data center supporting information and communication technologies such as smart phones has become a major energy consumer.The construction and operation of the data center has generated a large number of greenhouse gas emissions, which has brought enormous challenges to resources and the environment.
Talking about energy saving and consumption reduction of data center,The Ministry of Industry and Information Technology, the State Administration of Organs Affairs and the National Energy Administration jointly issued the Guiding Opinions on Strengthening the Construction of Green Data Centers,It is proposed that by 2022, the PUE value of new large and super large data centers in China should be below 1.4, as shown in Figure 3.
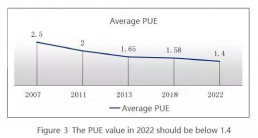
To achieve this goal, you need to first understand the proportion of energy consumption in PUE in the data center.Figure 4 shows the typical energy consumption distribution of the traditional data center machine room with PUE value=2,From the figure, we can not only visually observe the statistical distribution of power consumption of various electrical equipment in the data center machine room.In addition, it can also clearly indicate where its maximum energy saving potential lies in order to minimize the total energy consumption of the data center.The power consumption of IT equipment accounts for 50%, and the energy consumption of air-conditioning compressor refrigeration system ranks second.To reduce the PUE value, it is necessary to reduce the power consumption of auxiliary equipment such as refrigeration as much as possible.
Figure 4 Typical energy consumption distribution diagram of traditional data center machine room with PUE=2
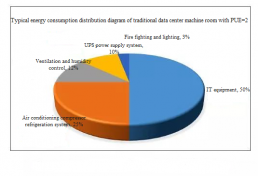
In view of the current development trend, Glacier Coolant Group has developed Glacier modified fluorinated liquid products, providing efficient and safe solutions for data centers, heating elements, electronic chips, etc. that need efficient heat dissipation.Glacier modified fluoride liquid is a highly stable perfluorinated liquid substance, which is colorless, tasteless, non-toxic, safe, insoluble in water, good thermal stability, and environmentally friendly.
Glacier modified fluoride liquid has a very moderate boiling point (about 50 ℃),High latent heat of vaporization(121.7 kJ/(kg·K),When immersed phase change liquid cooling is applied to data center server,Use the heat of evaporation tropics in the process of work,No air conditioning is required,The power consumption of the computer room is greatly reduced,Power Usage Effectiveness (PUE) is below 1.1,More than 85% energy saving compared with traditional air conditioning.Glacier modified fluoride liquid has excellent electrical insulation performance, with a dielectric strength of 55 kV, and will not cause damage to precision electronic instruments and equipment.At the same time, it has ideal chemical inertness, no ignition point, flash point, no combustion, no explosion, and good use safety.Glacier modified fluoride liquid also has excellent thermal conductivity, good fluidity and system compatibility. The ozone depletion potential (ODP) is 0, and the global warming potential (GWP) is 7. It is environmentally friendly, does not damage the ozone layer, and has wide applicability.
The typical schematic diagram of glacier modified fluoride liquid applied to the submerged liquid cooling system of the data center is shown in Figure 7.The server can be placed in a sealed cooling box with high density, and the main heat dissipation components of the server can be immersed in the glacier modified fluoride liquid. When the server is running, the heat dissipation parts generate a lot of heat to heat the modified fluoride coolant;As the boiling point of the coolant is low, it will immediately reach boiling, so that the coolant will be converted from liquid to gas, and the heat will be taken away by evaporation to achieve the effect of heat dissipation.The steam of the coolant condenses on the upper condenser into liquid and returns to the immersion liquid to realize recycling.
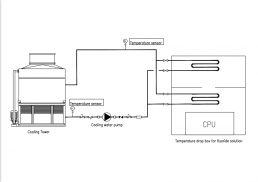
Glacier modified fluoride liquid directly contacts with various parts of the server, with fast heat transfer speed and energy saving of more than 85%;Simple equipment; It can realize high-density integration of servers, saving more than 80% of space; Both coolant and cooling water circulate in the system, so the loss of coolant and water is small and the operation cost is low.